ข้อบกพร่องประเภทหลักบนล้อรถไฟ
การ:แคลร์ เผยแพร่: 2567-05-20 ที่มา:www.train-wheels.com
สอบถาม
หัวรถจักรรถไฟและล้อรถ เป็นองค์ประกอบสำคัญในการรับประกันการปฏิบัติงานอย่างปลอดภัยของรถไฟ เนื่องจากรถไฟสามารถรับภาระและให้คำแนะนำได้หากล้อทำงานผิดปกติอาจทำให้ล้อร้าวและได้ แกน ตัดอาจทำให้รถไฟตกรางและเกิดอุบัติเหตุอย่างรุนแรงดังนั้นการตรวจจับและดูแลรักษาความปลอดภัยของล้อจึงมีความสำคัญอย่างยิ่ง
ข้อบกพร่องที่สำคัญในล้อรถไฟ
เมื่อรถไฟวิ่ง ช่วงความลึกที่แน่นอน (10 มม.~ 20 มม.) ใต้ ล้อรถไฟ พื้นผิวสัมผัสคือพื้นที่การกระจายสูงสุดของความเค้นเฉือนของการสัมผัสระหว่างรางล้อและหากมีข้อบกพร่องทางโลหะวิทยา เช่น การรวมตัวที่ไม่ใช่โลหะในบริเวณนั้น การรวมเข้าด้วยกันจะกลายเป็นแหล่งที่มาของรอยแตกเมื่อยล้าภายใต้การกระทำของความเค้นเฉือน จากนั้น รอยแตกเมื่อยล้ายังคงขยายตัวต่อไป
ความเค้นเฉือนจากการสัมผัสระหว่างรางล้อและรางนั้นมีอยู่ในคู่ล้อเมื่อรถไฟกำลังทำงาน เมื่อแหล่งกำเนิดรอยแตกเกิดนิวเคลียสและกระตุ้นให้รอยแตกแตกหน่อภายใต้การกระทำของความเค้นเฉือน ยิ่งรถไฟวิ่งเร็วเท่าไร การขยายตัวของรอยแตกก็จะเร็วขึ้นเท่านั้น เมื่อรอยแตกร้าวขยายใหญ่ขึ้นในระยะการขยายตัวอย่างรวดเร็ว รอยแตกร้าวจะพัฒนาไปที่ขอบนอกของขอบล้อ ด้านใน หรือพื้นผิวดอกยาง เช่น ตรวจไม่พบทันเวลาจะส่งผลให้ล้อ 'บล็อกล้ม หาก ตรวจไม่พบทันเวลา จะทำให้ล้อ 'หลุดออกจากบล็อก'ข้อบกพร่องประเภทนี้เรียกว่าขอบร้าว
รอยแตกเมื่อยล้าบนขอบล้อราง
ขอบล้อรถไฟหลุด
จากข้อบกพร่องรอยแตกร้าวของขอบล้อแบบเปิด เห็นได้ชัดว่าข้อบกพร่องรอยแตกร้าวของขอบล้อนั้นมีสาเหตุมาจากความล้าและกระบวนการขยายความล้า (รอยแตกของเปลือก)จากกระบวนการพัฒนาขอบล้อแตกร้าวขยายไปตามเส้นรอบวงล้อจึงเรียกว่าข้อบกพร่องตามเส้นรอบวง
การบิ่นของล้อในแนวรัศมีเนื่องจากการเบรกอย่างแรงผิดปกติ ข้อบกพร่องด้านโลหะวิทยาภายในล้อ หรือข้อบกพร่องในกระบวนการผลิตอาจทำให้รถไฟพลิกคว่ำในการทำงานของรถไฟ

ล้อรถไฟแตกตามทิศทางของเส้นผ่านศูนย์กลางล้อ เรียกว่าข้อบกพร่องในแนวรัศมี
กระบวนการตรวจจับข้อบกพร่องด้วยอัลตราโซนิกสำหรับข้อบกพร่องของล้อรถไฟ
ตามหลักการของการตรวจจับข้อบกพร่องล้ำเสียง พลังงานสะท้อนล้ำเสียงจะสูงสุดเมื่อคลื่นอัลตราโซนิกตั้งฉากกับพื้นผิวรอยแตกคลื่นอัลตร้าโซนิคที่ตกกระทบตามทิศทางรัศมีของล้อจะตั้งฉากกับข้อบกพร่องของเส้นรอบวงอย่างแน่นอนดังนั้นการใช้การตรวจจับอุบัติการณ์อุบัติการณ์อัลตราโซนิคของข้อบกพร่องเส้นรอบวงล้อ
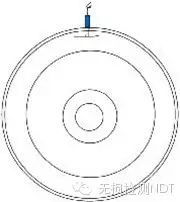
การตรวจจับโดยใช้คลื่นตามขวางอัลตราซาวนด์ธรรมดา
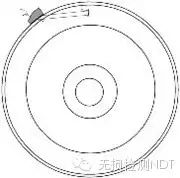